The ALD system C2R of the Finnish ALD equipment supplier Beneq achieves speeds of up to 200 rpm with deposition rates of up to 1 µm/hour. ALD is a self-limiting and isotropic process, producing approximately 1 Angstrom of layer thickness per cycle. This allows immense control over the film thickness and the ability to deposit highly conformal films on complex 3D objects and nanostructures, like for example waveguides, lenses and domes.
Significant reduction of coating times
The heart of the spatial ALD system is a turntable that eliminates the need for temporally separated gas dosing as used in batch ALD systems. Instead, pressure and nitrogen curtains geometrically separate four zones within the system. One rotation of the turntable corresponds to one cycle of ALD, exposing the samples to necessary reactants at separate points during the rotation. Without lengthy purge steps, the spatial ALD-system reduces coating times significantly compared to traditional thermal ALD processes, making the tool capable of production scale ALD coatings.
Coating complex objects: simple and fast
Beneq has developed the system together with LZH to meet the needs for emerging optical coatings. “We were surprised by its [ALD] simple adaptation to optical coatings,” says LZH’s Head of Optical Components Department, Dr. Andreas Wienke. “For example, think of a strongly curved, small aspheric lens. With classical PVD processes, it is nearly impossible to achieve a conformal coating on the curved surface and the same reflection or transmission values over the whole area. With ALD, it seems so simple and easy to achieve.”
Broadband monitoring for precise and reproducible coatings
LZH’s own in-situ monitoring tool has been implemented recently to improve the C2R’s capabilities. “The broadband monitoring system BBM of the LZH takes complex coatings to the next level. The high-resolution monitoring of the layer growth allows not only to measure online but also to re-engineer the coating on-the-fly, yielding very precise and reproducible thin films”, explains Sami Sneck, VP of Advanced ALD at Beneq. “With the new BBM and loadlock additions, we are glad to offer a highly-effective tool to our customers, making ALD even more reliable for optical coatings.”
Spatial ALD matches PVD processes like Ion Beam Sputtering in many aspects, including speed and optical performance. It can play to its full advantage when it comes to coating complex shapes and nanostructures. It therefore offers economical and reliable coatings for use in mobile phone cameras or LIDAR systems in self-driving vehicles. Currently, the LZH is working on coating optical grating structures and polymer optical lenses for use in virtual and augmented reality glasses with the spatial ALD approach.
This video gives a deeper insight into the cooperation between LZH and Beneq.
Partner
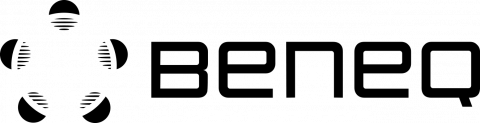
Laser Zentrum Hannover e.V. (LZH)
As an independent, non-profit research institute, the Laser Zentrum Hannover e.V. (LZH) stands for innovative research, development, and consulting. Supported by the Lower Saxony Ministry of Economics, Transport, Construction and Digitalization, the LZH is dedicated to selflessly promoting applied research in the field of photonics and laser technology. Founded in 1986, almost 200 employees are now working at the LZH.
The LZH offers solutions to current and future challenges with its smart photonics. Along the process chain, natural scientists and engineers work interdisciplinary together: from component development for specific laser systems or for quantum technologies to process developments for a wide variety of laser applications, for example for medical and agricultural technology or lightweight construction in the automotive sector. 18 successful spin-offs have emerged from the LZH to date. Thus, the LZH creates a strong transfer between fundamental science, application-oriented research, and industry - and uses light for innovation.
Beneq Oy
Beneq is the home of atomic layer deposition. In 1984, we established the world’s first industrial production using ALD. Today, we lead the market with products for R&D (TFS200, TFS500, R2), semiconductor device fabrication (Transform®, Transform® 300, and ProdigyTM), 3D and batch production (P400A, P800, P1500), ultra-fast spatial ALD (C2R), and roll-to-roll ALD (Genesis).
Beneq’s unique Development Service simplifies customer adoption and proof-of-concept for new ALD processes, while our Coating Service cuts down time to market by outsourcing state of the art ALD production. Our team of engineers and experts is dedicated to making ALD tools accessible for researchers.