Steel components from the 3D printer: deposition welding in XXL format
Manufacturing individual large-scale components is usually an energy- and material-intensive affair. In the "XXL3DDruck" project, scientists at the Laser Zentrum Hannover e.V. (LZH) have joined forces with partners to test a more resource-efficient way of producing XXL components. To this end, they produced parts of a ship gearbox housing with a mass of up to three tons layer by layer in an oversized 3D printer using a laser-assisted arc welding process.
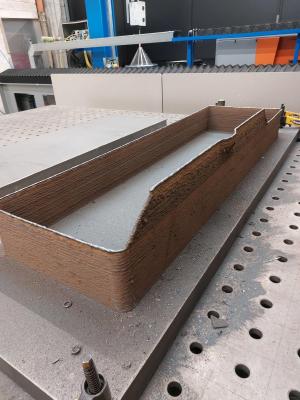
XXL 3D printing to save energy and material in production
The XXL printer with an installation space of 3 x 4.5 meters, which is used as a prototype for research and development purposes only, is located at the marine gearbox manufacturer REINTJES in Hameln. It uses laser-assisted arc deposition welding, a high-performance additive process method for metals that achieves high mass throughput. The consortium can apply up to 3.2 kilograms of steel per hour with the printer.
The process can reduce the use of material and energy compared to conventional manufacturing methods: Classically, individual molds are made for the components of marine gearbox housings. This work step is eliminated in Additive Manufacturing. Material and weight can also be saved because components can be redesigned and constructed differently - with hollow walls, for example. Laser-assisted arc deposition welding can also implement individual, component, and customer-specific design requirements.
Resources are also saved in ship operation
XXL printing conserves resources during production and later during the operation of the ship - if less material is used, the ship has to accelerate less mass and thus also requires less fuel.
A part of a ship's gearbox housing, which is currently still being manufactured, serves as a demonstrator. Through Additive Manufacturing, the project participants would like to reduce the weight of a ship gearbox housing by several tons. The long-term goal for production is to reduce manufacturing and procurement time as well as to save raw materials such as steel by reducing the amount of material used per housing.
About XXL3DDruck
The joint project „XXL3DDruck: Energie- und ressourceneffiziente Herstellung großskaliger Produkte durch additive Fertigung am Beispiel von Schiffgetriebegehäusen“ was funded by the German Federal Ministry for Economic Affairs and Climate Action under the funding code 03ET1644C (duration 2019 - 2023).
The project was managed by REINTJES GmbH. The LZH was responsible for the development of the process technology. EILHAUER Maschinenbau GmbH took over the plant engineering of the XXL 3D printer. TEWISS - Technik und Wissen GmbH was responsible for building the print head and controlling the printer. The IPH - Institut für Integrierte Produktion Hannover gemeinnützige GmbH developed an inline measurement technology for process monitoring.
Laser Zentrum Hannover e.V. (LZH)
As an independent, non-profit research institute, the Laser Zentrum Hannover e.V. (LZH) stands for innovative research, development, and consulting. Supported by the Lower Saxony Ministry of Economics, Transport, Construction and Digitalization, the LZH is dedicated to selflessly promoting applied research in the field of photonics and laser technology. Founded in 1986, almost 200 employees are now working at the LZH.
The LZH offers solutions to current and future challenges with its smart photonics. Along the process chain, natural scientists and engineers work interdisciplinary together: from component development for specific laser systems or for quantum technologies to process developments for a wide variety of laser applications, for example for medical and agricultural technology or lightweight construction in the automotive sector. 18 successful spin-offs have emerged from the LZH to date. Thus, the LZH creates a strong transfer between fundamental science, application-oriented research, and industry - and uses light for innovation.