Smart additive
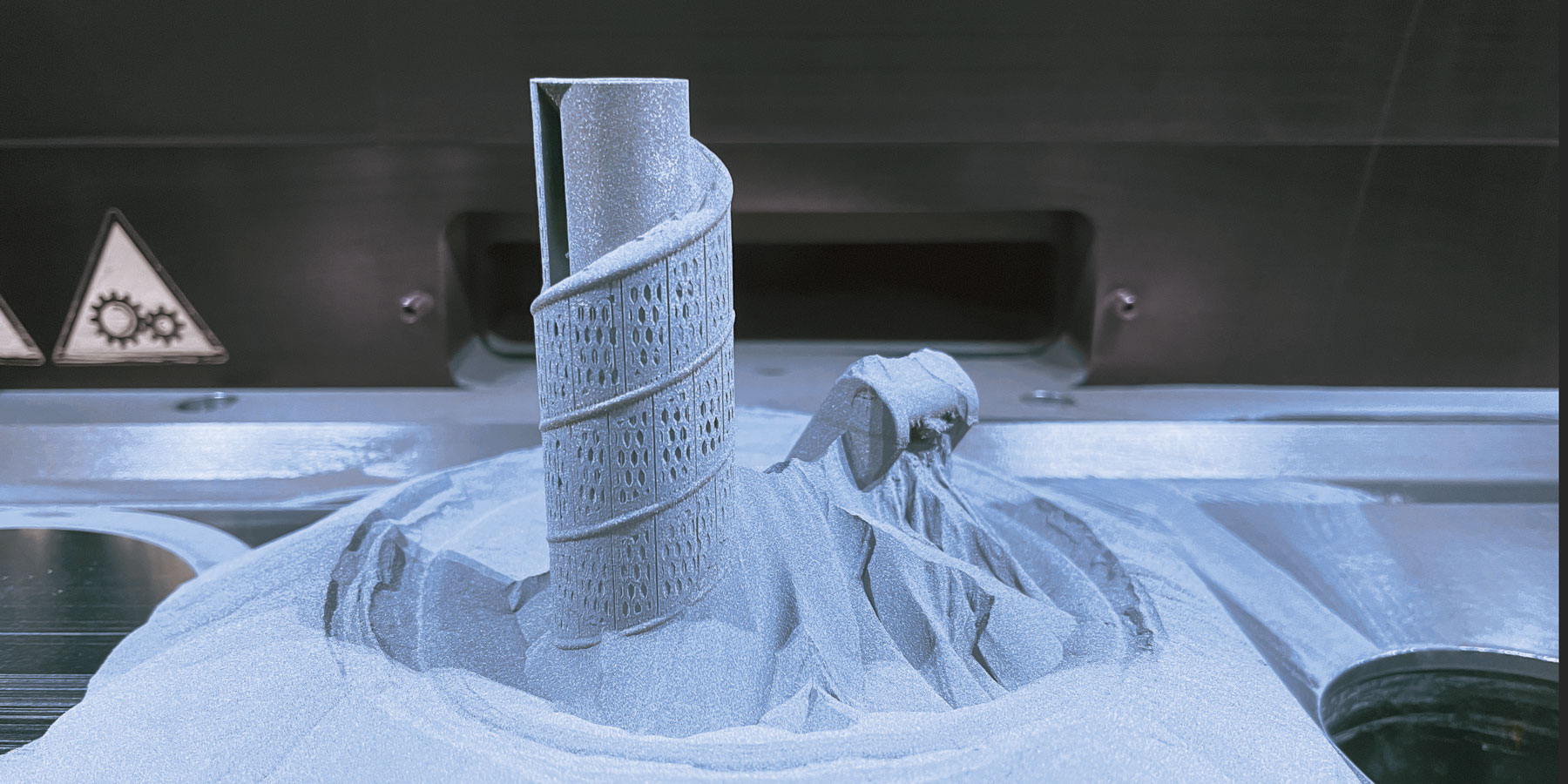
Smart Additive Manufacturing enables new approaches to production. It allows novel shapes and functions. We are constantly developing and optimizing processes for additive manufacturing, opening up technologies for processing new materials and thus enabling additive manufacturing processes to be established in production. We automate processes and process chains and integrate them into existing systems. Intelligent process monitoring, in interaction with digital twins and artificial intelligence, will allow corrections to be made in the running printing process in the future.
Your contact person
Dr.-Ing. SFI Jörg Hermsdorf
Overview of smart additive
Metal
Laser-additively manufactured components made of metal are robust and have similar, sometimes even higher strengths than conventionally manufactured components. Skillful design and function integration enable material, time, and effort to be minimized. In addition to the familiar powder- and wire-based processes, we are also working on novel process and material combinations and on exploring the limits of what can be printed.
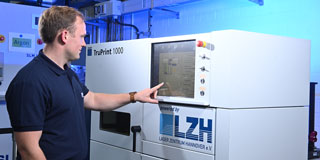
With Powder Bed Fusion (LPBF/PBF-LB/M), we produce components with mechanical properties equivalent to their conventionally manufactured counterparts. We are constantly developing the underlying processes and are engaged in the production of very small and very large components as well as in topology optimization for these components. We work with industrially proven titanium, CrNi, copper, and wear and corrosion-resistant steel alloys. In addition, we are establishing 3D printing processes for magnesium alloys, Kovar, regolith, and other special materials.
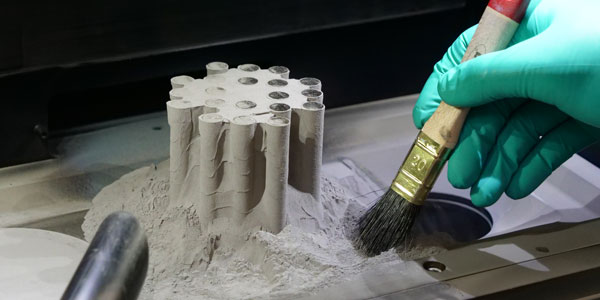
New materials with new possibilities are crucial for innovative applications in lightweight construction or medical technology. We research processes for these materials and characterize them for additive manufacturing. For oxygen-affine materials, for example, we develop plant and machine technology with oxygen-free environments. For special materials, we adapt the processes to the application. In addition, we work with statistical experimental design to smartly expand process windows and investigate the interrelationships of various target variables.
- Titanium alloys
- Magnesium alloys
- Kovar
- Invar
- Nickel-titanium alloys
- Nickel superalloys
- Copper alloys
- Regolith
- Wear and corrosion-resistant steel alloys
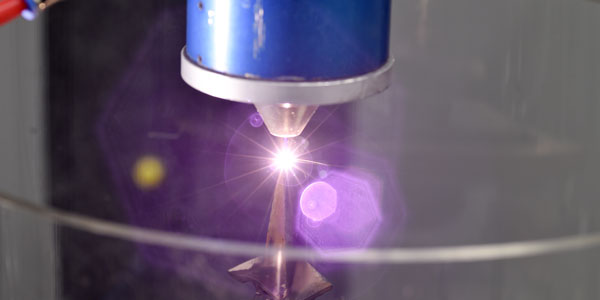
Powder-based deposition welding is suitable for building new structures as well as for repairing high-cost components. To repair high-temperature materials in the same way, we are researching single-crystal deposition welding. With various nickel base superalloys we work on repairing engine components and transfer this method to technical applications. Also, we are developing future-relevant processes for thermal and structural components made of different material combinations and engaged in alloying and dispersing ceramic particles and grading with tungsten carbides.
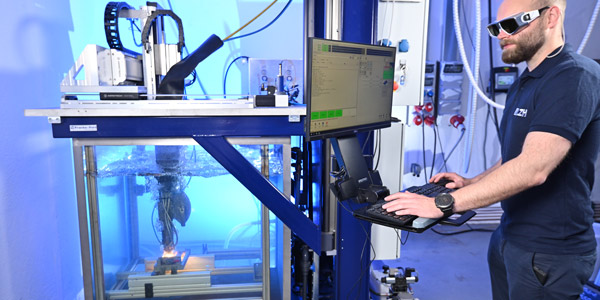
Whether underwater or under varying gravity conditions, we make additive manufacturing possible even under challenging environmental conditions. To this end, we are developing the necessary process and system technology. This must also function robustly under different pressure conditions to implement repairs or add-ons to maritime systems with additive manufacturing in the future. To make this possible, we take into account the water depth and the ambient temperature and the nature of the materials present.
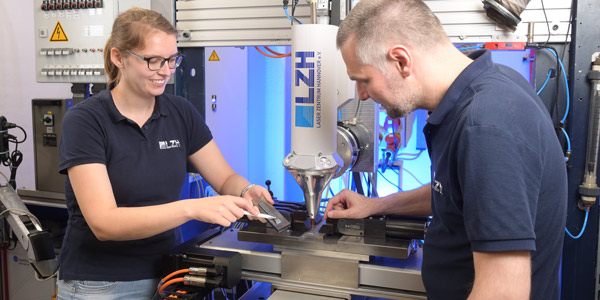
Deposition welding with wire as the filler material is an efficient and fast process. We develop processes for this welding technique with structure sizes in the micrometer range up to XXL products with several tons of component weight. We use laser-wire deposition welding and laser-assisted processes with and without arc and with one or two wires. We work with wire diameters from 0.1 mm to 1.6 mm and print, for example, wear-resistant steel alloys such as 100Cr6. The processes are suitable, for example, for thermally and mechanically highly stressable prototypes, tool and mold making and for products/small series. We are also working on producing semi-finished products for subsequent forming.
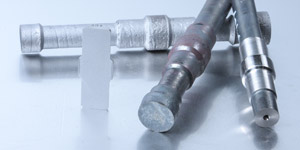
For complex components, we combine several processes to manufacture across scales. This results in components that combine the advantages of several manufacturing techniques. For example, our scientists print large basic bodies and supplement them with filigree structures. In hybrid manufacturing, we work with different materials to apply wear or corrosion protection. Also, our team adjusts the properties of the manufactured structures with in-situ alloys. Furthermore, we investigate graded structures to optimize material transitions and make scale-independent and modular production technology possible.
Polymer
Additive Manufacturing with polymers and plastics is already used industrially but still holds enormous potential. Therefore, we are optimizing processes to open up new applications or are working on establishing new materials to make plastic printing more sustainable. To manufacture components even better and more cost-effectively, we are also working on process stability and component resolution.
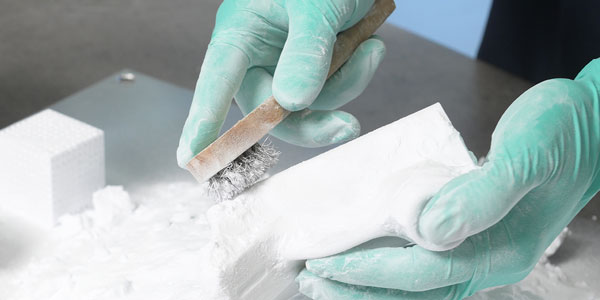
We are working on smart process monitoring systems for selective laser melting (SLS). These should make it possible to intervene in the running process and adjust it if necessary. In this way, we want to prevent heat buildup and make the entire powder bed reliably usable as a printing area. In this way, we want to avoid costly and time-consuming misprints. We continue to develop powder-based additive manufacturing processes with the laser to adapt them for new applications or materials.
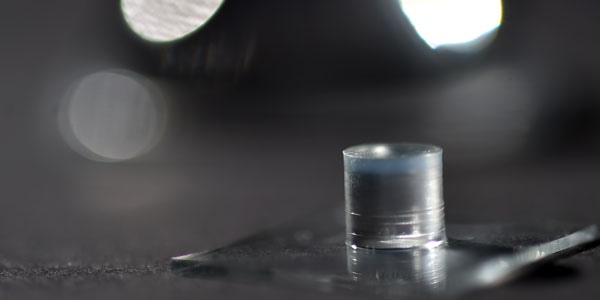
Few products consist of only one material. To additively manufacture multi-material components, we are developing processes to combine different materials. On the one hand, the focus is on combining materials of the same type, and on the other hand, on combining metal components with plastics. We are also working on graded materials to flexibly vary the hardness and composition of a component.
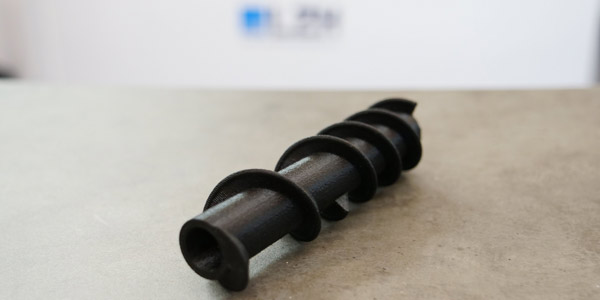
In Fused Deposition Modelling (FDM), we focus on topology optimization and process development to qualify new materials for 3D printing. One focus is on sustainable natural fiber-based or compostable materials. With high-performance fiber composite structures, we want to create new manufacturing processes for lightweight construction. We are also working on joining 3D-printed elements through laser transmission welding. Components made by filament printing have many uses, including facade cladding in architecture or as veneers on furniture. We work in particular on:
- fiber composite structures
- short and continuous fiber-reinforced materials
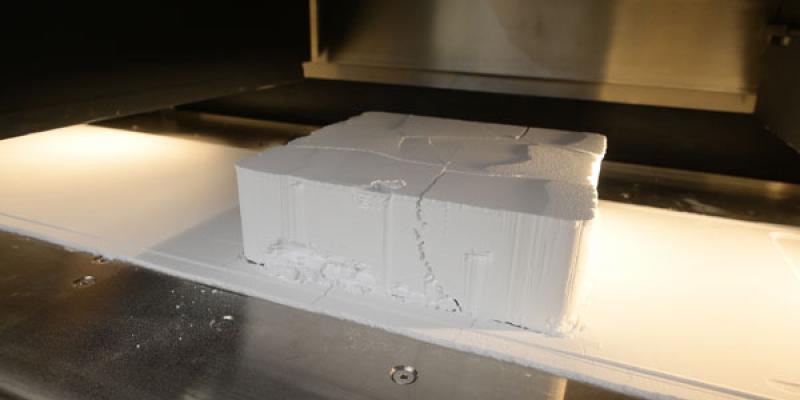
To further establish Additive Manufacturing in the industry and to open up new application fields, we are working on and with new materials. To this end, we develop new processes or optimize existing ones. To achieve optimal properties, we analyze and characterize the components in detail and adapt the processes accordingly. We work with:
- conductive materials
- sustainable and compostable natural materials
- carbon fibers for fiber composite structures
- transparent photopolymers
- hybrid materials (organic-inorganic)
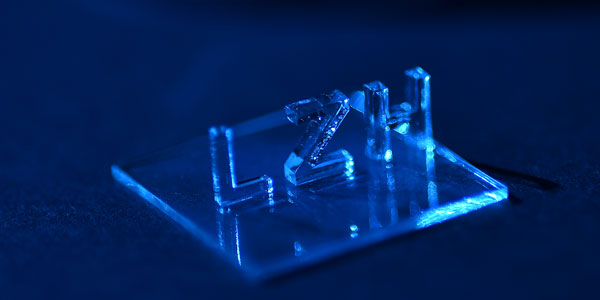
We develope high-resolution 3D printing processes further to tap their potential for the generative production of multiscale structural parts or even complex components. In addition to laser-based technologies in the polymer bath, such as stereolithography and two-photon polymerization, we use micro-dispensers and the Aerosol Jet as well as hybrid processes. We dispense conductive tracks and optical polymers, for example. Additionally, to expand the potential for industrial use, we are developing strategies for automating process chains.
Glass & ceramic materials
Additive manufacturing of glass and ceramic materials will open up new fields of application in the future, for example in chemical apparatus engineering, architecture, or even optics. Therefore, we develop manufacturing processes further to produce reproducible and automatable glass components with a high level of complexity and optical quality.
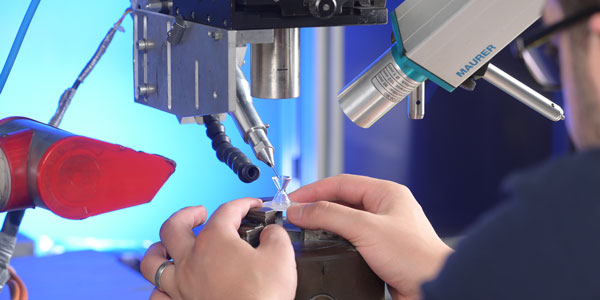
The Additive Manufacturing of glass, also known as Laser Glass Deposition, has been co-developed by us and enables the automated production of complex structures using a fiber-based process. The focus is on the automation of extensive handling, from handling the raw material to the finished product for standardized, reproducible results. Furthermore, we are working on additive manufacturing of optics and optical components such as ball lenses. We can print on existing components as well as build up independent components layer by layer.
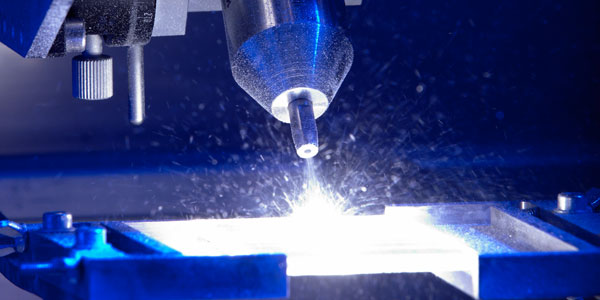
Ceramic and glass materials can be additively processed into components using the powder bed process. In addition to producing complete components, we are researching the targeted modification of electrical properties by dispersing ceramic particles in metal during laser cladding. We are also working on grading with tungsten carbides in the laser coating process to significantly improve the service life of tools.
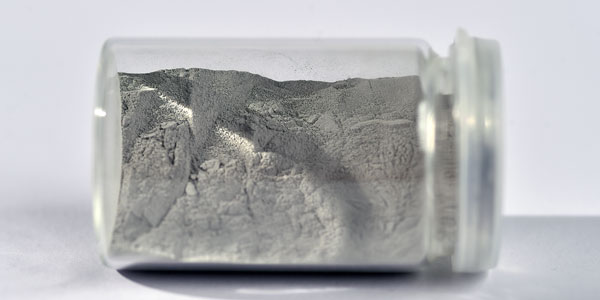
To set the basis for more applications for the additive manufacturing of glasses and ceramics, we are developing and evaluating processes for materials that have not yet been used for this purpose. The processing of quartz glass and borosilicate glass is of great interest for optics and glass apparatus engineering. For ceramic and glass materials, we are currently developing the processes further. We are also working on enabling additive processing of the widely used soda-lime glass for the first time.
Construction & product design
Additive Manufacturing processes overcome many design limitations. However, not every design is suitable for Additive Manufacturing. We develop smart designs and optimize components that fully exploit the possibilities of additive manufacturing and are optimized in terms of material and effort. We also work on optomechanics.
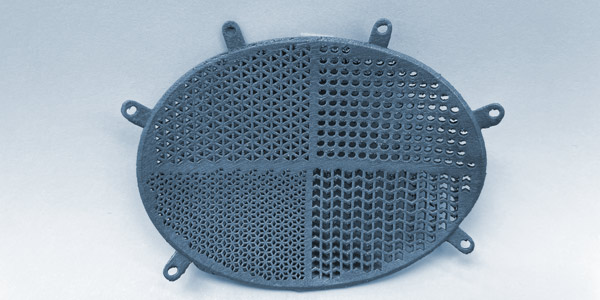
Additive Manufacturing enables almost complete design freedom. But every additive process has its own peculiarities that must be considered in the design of individual components to keep material, printing times, and post-processing to a minimum. Therefore, we work on the smart design of components, their optimal alignment in the installation space, and the optimal use of support structures.
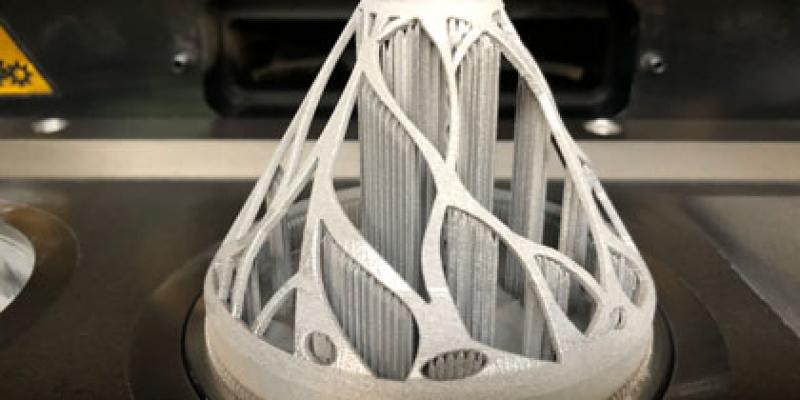
Saving material and weight and reducing printing times while maintaining load capacity - topology optimization is worthwhile for many components. We calculate the best distribution of forces and optimize the use of materials. Our team also deals with automated solutions to combine topology optimization with design guidelines in the future and arrive at the best product design of an individual component.
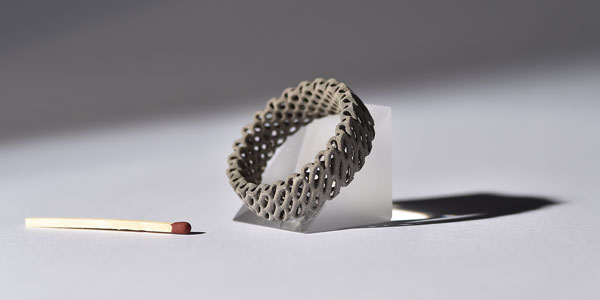
For lightweight construction from the 3D printer, we develop processes with materials such as magnesium and optimize the design through clever construction and topology optimization. Magnesium is mechanically resilient, bioresorbable and yet has a low density. It is also particularly suitable for use in internal structures. Our scientists are also involved in developing and optimizing processes for material combinations that are difficult to process and making them suitable for industrial use.
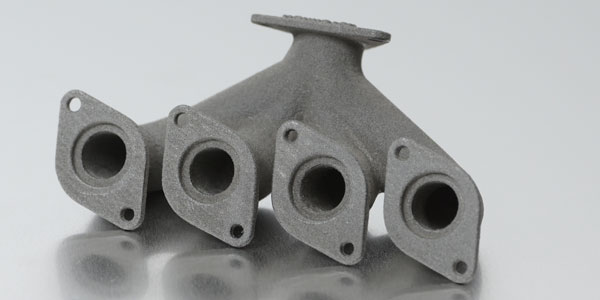
Cooling channels directly on the contour, with curves and angles or internal mounting - Additive Manufacturing allows functions to be optimally integrated into components. We optimize components for additive manufacturing and develop the appropriate processes. In the process, we also look at how special new components can be designed. A new component can combine several individual components.
Plant and system technology
Processes are often only as good as the equipment on which they run. Therefore, we constantly develop plant and system technology considering their specific applications and integration into existing plants and industrial readiness. Our spectrum ranges from individual system components to plant components or complete machines.
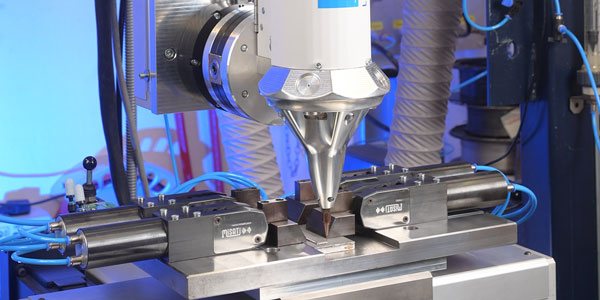
We complement our process development with self-developed laser processing heads to find the best solutions for innovative applications - ready for industrial applications. Our developments to date include coaxial processing heads for deposition welding, which can process various materials independently of the direction. In doing so, we constantly incorporate findings from research into the further development of the system components.
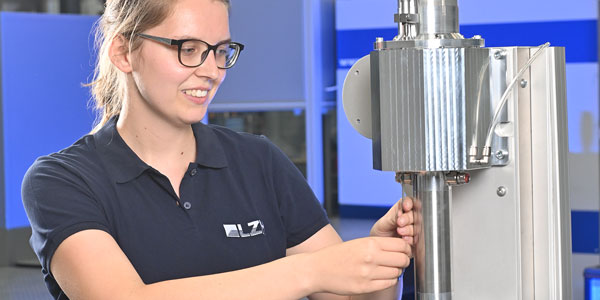
Additive Manufacturing processes rarely stand alone in the production environment. We work on the integration and connection of our developed components into existing machines and systems. Our scientists also conduct research into combining processes with one another. For example, our team is working with machines that combine additive and subtractive processes for faster production and shorter downtimes. Furthermore, we are working on making production possible in an oxygen-free environment.
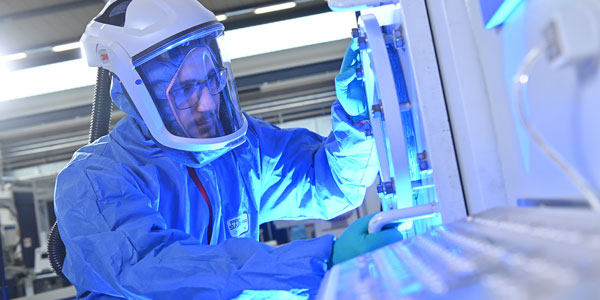
Additive Manufacturing brings new challenges for plant and occupational safety. We develop strategies for the safe handling of powders or conveyor lines for integration into production and deal with the monitoring of process emissions. Our focus lays on the preventing the carryover of powder particles. For this, our scientists investigate the carryover even up to bringing it into homes and show solutions to circumvent it.
Monitoring and quality assurance
We are researching smart process monitoring with real-time control for production with as few errors and rejects as possible. This should make additive manufacturing more reliable, more cost-effective, and thus even more attractive. We use non-destructive characterization and analysis methods, enabling us to match components with their digital twin and further improve processes with the help of artificial intelligence. Process monitoring and quality assurance are thus an essential part of our research for the "first-time-right" strategy.
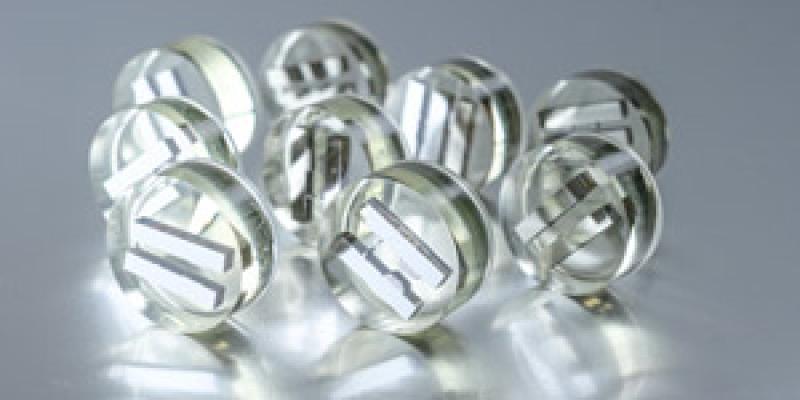
To consistently increase the quality of additively manufactured components, we develop appropriate characterization methods for powders and components. Before printing, our team examines powders for their particle shape and size and their bulk density and tap density. We analyze finished components for pore formation, layer thickness, and suitability using various methods, including hardness tests. Also, our scientists develop non-destructive analyses using optical coherence tomography (OCT) and emission analyses. We also have scanning electron microscopy (SEM), a nano-computer tomograph, and energy dispersive X-ray spectroscopy (EDX) at our disposal. In combination with online process control, we thus aim to implement a "first-time-right" strategy, i.e. additive manufacturing with as little scrap as possible.
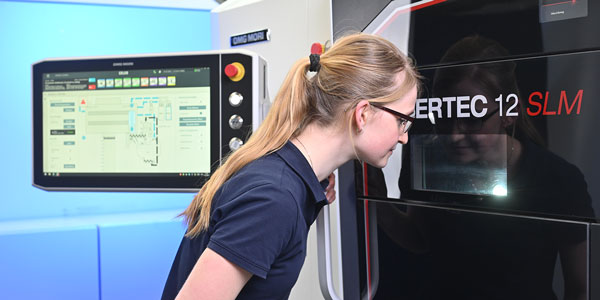
By monitoring the ongoing printing process, we want to be able to intervene flexibly in the printing process in the future and make adjustments. Our scientists are developing monitoring systems further and are looking into their integration into the printing processes and post-processing. We use:
- hyperspectral cameras for detect impurities and predicting the roughness of surfaces
- pyrometry and thermography
- measure oxygen content.
In the future, the goal is to detect defects directly as the layers are formed and thus compensate for defective areas. For this, our scientists develop feedback loops and using artificial intelligence to realize scrap-free additive manufacturing.
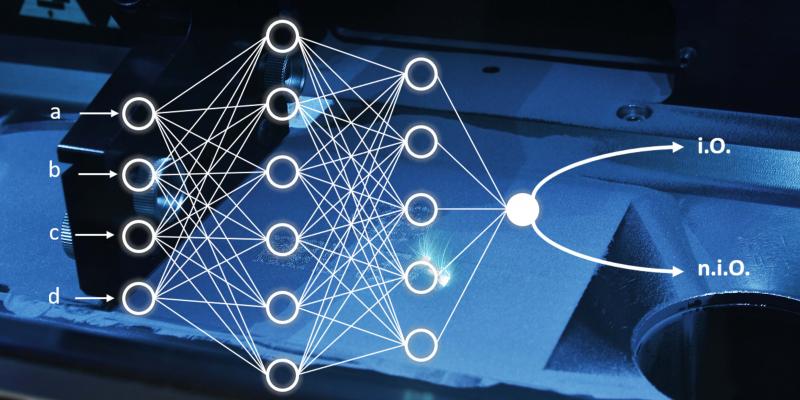
The added value of artificial intelligence in Additive Manufacturing goes far beyond monitoring. We are working on self-learning systems that will actively control the process in the future and thus avoid or compensate for errors. The basis for this is a deep understanding of the process and the comprehensive recording of process data. Machine learning can classify components and predict surface roughness using image processing and feature recognition.