Smart Additiv
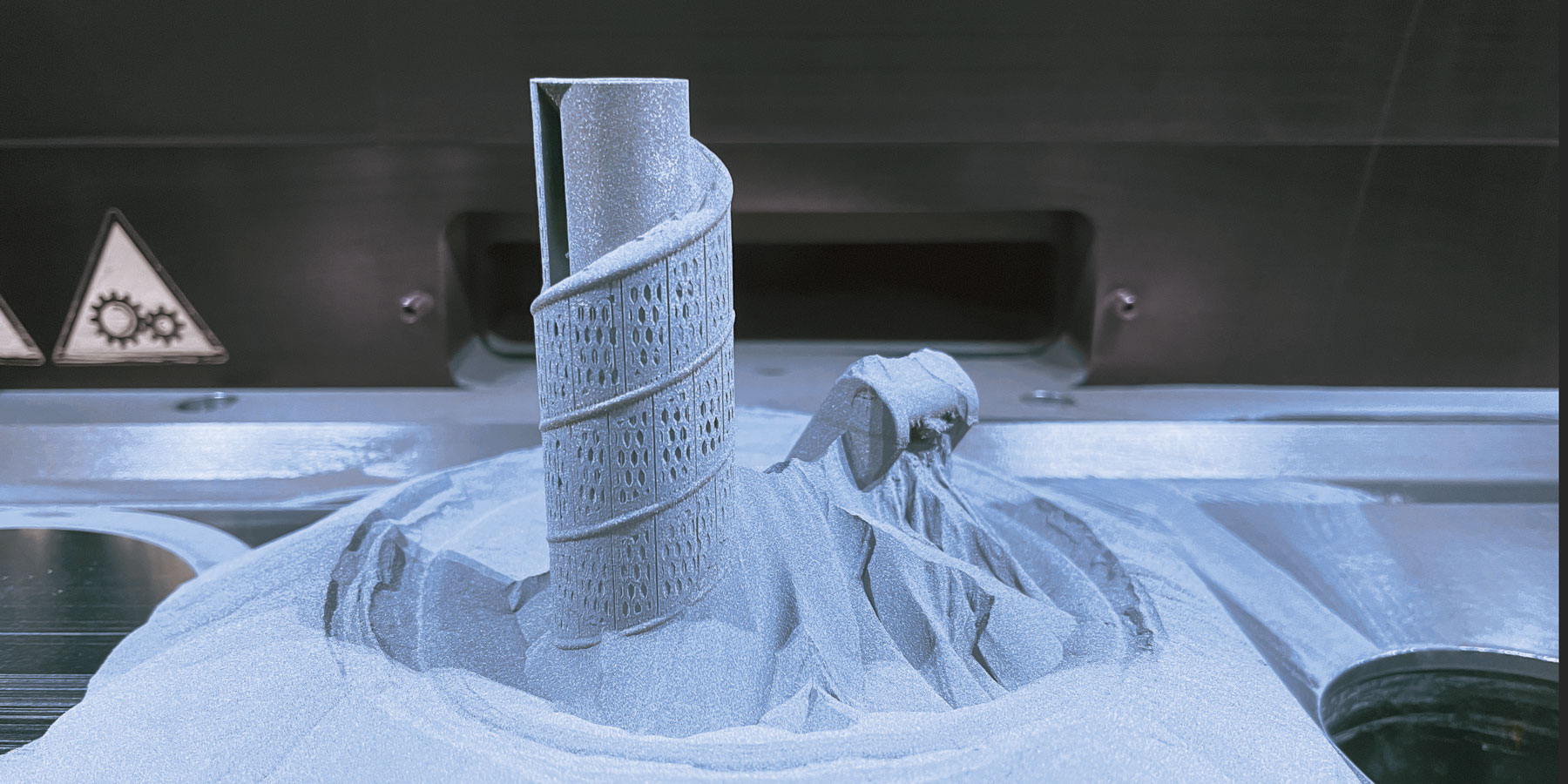
Smarte Additive Fertigung ermöglicht neue Herangehensweisen an die Produktion. Sie erlaubt neuartige Formen und Funktionen. Wir entwickeln und optimieren Prozesse für die Additive Fertigung beständig weiter, erschließen Technologien zur Verarbeitung neuer Materialien und ermöglichen so, additive Fertigungsprozesse in der Produktion zu etablieren. Wir automatisieren Prozesse und Prozessketten und integrieren diese in bestehende Systeme. Intelligente Prozessüberwachungen, im Zusammenspiel mit digitalen Zwillingen und künstlicher Intelligenz, erlauben zukünftig Korrekturen im laufenden Druckprozess.
Ihr Kontakt
Nick Schwarz, M. Sc.
Smart Additiv in der Übersicht:
Metall
Laser-additiv gefertigte Bauteile aus Metall sind robust und haben ähnliche, teilweise sogar höhere Festigkeiten als konventionell gefertigte Bauteile. Geschickte Konstruktion und Funktionsintegration ermöglichen, Material, Zeit und Aufwand zu minimieren. Wir arbeiten neben den bekannten Pulver- und Draht-basierten Verfahren auch an neuartigen Verfahrens- und Werkstoffkombinationen und daran, die Grenzen des Druckbaren auszuloten.
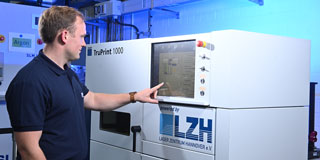
Mit der Additiven Fertigung im Pulverbett (eng: Laser Powder Bed Fusion; LPBF/PBF-LB/M) stellen wir Bauteile her, deren mechanische Eigenschaften ihren konventionell gefertigten Pendants gleichkommen. Wir entwickeln die zugrundeliegenden Prozesse beständig weiter und beschäftigen uns mit der Fertigung von sehr kleinen und sehr großen Bauteilen sowie mit der Topologieoptimierung für diese Bauteile. Wir arbeiten mit industriell erprobten Titan-, CrNi-, Kupfer- und Verschleiß- und korrosionsbeständigen Stahllegierungen. Zudem etablieren wir 3D-Druckprozesse für Magnesiumlegierungen, Kovar, Regolith und weitere Sondermaterialien.
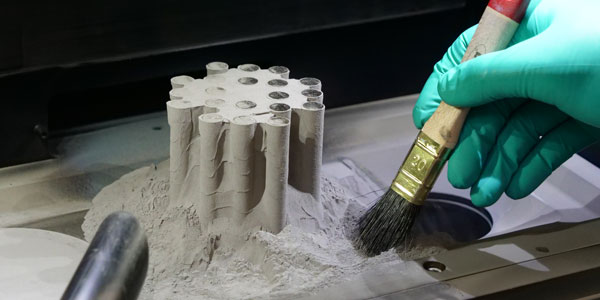
Neue Werkstoffe mit neuen Möglichkeiten sind für innovative Anwendungen im Leichtbau oder der Medizintechnik entscheidend. Wir erforschen Prozesse für diese Werkstoffe und charakterisieren diese für die Additiven Fertigung. Für Sauerstoff-affine Werkstoffe entwickeln wir zum Beispiel Anlagen- und Maschinentechnik mit sauerstofffreien Umgebungen. Für Sondermaterialien passen wir die Prozesse auf den Einsatz an. Zudem arbeiten wir mit statistischer Versuchsplanung, um Prozessfenster smart zu erweitern und die Zusammenhänge verschiedener Zielgrößen zu untersuchen.
• Titanlegierungen
• Magnesiumlegierungen
• Kovar
• Nickel-Titanlegierungen
• Nickelsuperlegierungen
• Kupferlegierungen
• Regolith
• Verschleiß- und korrosionsbeständige Stahllegierungen
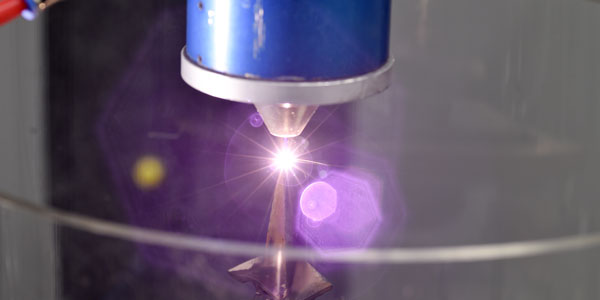
Pulver-basiertes Auftragschweißen eignet sich sowohl für den Aufbau neuer Strukturen als auch für die Reparatur von kostenintensiven Komponenten. Wir erforschen das einkristalline Auftragschweißen, um Hochtemperaturwerkstoffe artgleich zu reparieren. Für die Reparatur von Triebwerkskomponenten setzen wir verschiedene Nickelbais-Superlegierungen ein und transferieren diese Methode in die technische Anwendung. Zudem entwickeln wir zukunftsrelevante Prozesse für thermische und strukturelle Komponenten aus verschiedenen Materialienkombinationen. Außerdem beschäftigen wir uns mit dem Legieren und Dispergieren von Keramikpartikeln und dem Gradieren mit Wolframkarbiden.
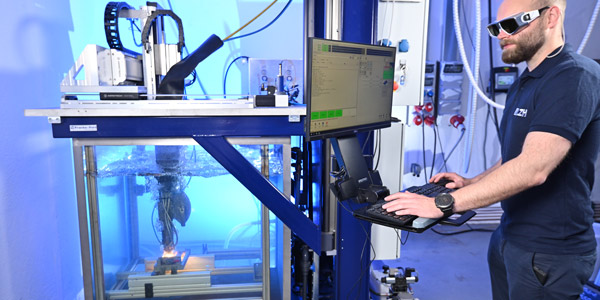
Ob unter Wasser oder Schwerkraftbedingungen - wir arbeiten daran, die Additive Fertigung selbst unter schwierigen Umgebungsbedingungen möglich zu machen. Dafür entwickeln wir die erforderliche Prozess- und die Systemtechnik. Diese muss auch bei unterschiedlichen Druckverhältnissen robust funktionieren, um zukünftig Reparaturen oder Anbauten an maritimen Anlagen mit der Additiven Fertigung umsetzen zu können. Um dies zu ermöglichen, berücksichtigen wir neben der Wassertiefe auch die Umgebungstemperatur sowie die Beschaffenheit der vorliegenden Materialien.
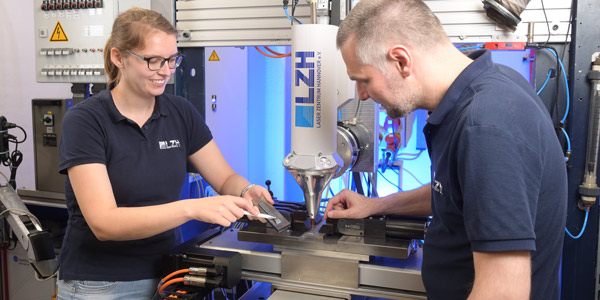
Auftragschweißen mit Draht als Ausgangsmaterial ist ein effizientes und schnelles Verfahren. Wir entwickeln Prozesse zum Auftragschweißen mit Strukturgrößen im Mikrometerbereich bis hin zu XXL- Produkten mit mehreren Tonnen Bauteilgewicht. Wir setzen dazu das Laser-Draht-Auftragschweißen sowie Laser-unterstützte Verfahren mit und ohne Lichtbogen sowie mit einem oder zwei Drähten ein. Wir arbeiten mit Drahtdurchmessern von 0,1 mm bis 1,6 mm und drucken beispielsweise verschleißbeständige Stahllegierungen wie 100Cr6. Die Verfahren eignen sich etwa für thermisch sowie mechanisch hochbelastbare Prototypen, Werkzeug- und Formenbau und für Produkte/Kleinserien. Ebenso arbeiten wir daran, Halbzeuge für späteres Umformen herzustellen.
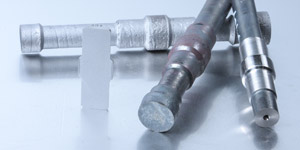
Für komplexe Bauteile kombinieren wir mehrere Verfahren, um skalenübergreifend zu fertigen. So entstehen Bauteile, die die Vorteile mehrerer Fertigungstechniken vereinen, zum Beispiel drucken wir große Grundkörper und ergänzen sie mit filigranen Strukturen. In der hybriden Fertigung arbeiten wir mit verschiedenen Materialien, um Verschleiß- oder Korrosionsschutz aufzubringen. Außerdem beschäftigen wir uns mit In-Situ-Legieren, um bedarfsgerecht die Eigenschaften der gefertigten Strukturen einzustellen. Weiterhin arbeiten wir an gradierten Strukturen, um Materialübergänge zu optimieren und beschäftigen uns damit, skalenunabhängige und modulare Produktionstechnik möglich zu machen.
Polymer
Additive Fertigung mit Polymeren und Kunststoffen wird zwar bereits industriell eingesetzt, birgt aber noch enormes Potential. Daher optimieren wir Prozesse, um neue Einsatzmöglichkeiten zu erschließen oder arbeiten daran neue Werkstoffe zu etablieren, um beispielsweise den Kunststoff-Druck nachhaltiger zu machen. Um Bauteile noch besser und kostengünstiger herstellen zu können, arbeiten wir außerdem an der Prozessstabilität und Bauteilauflösung.
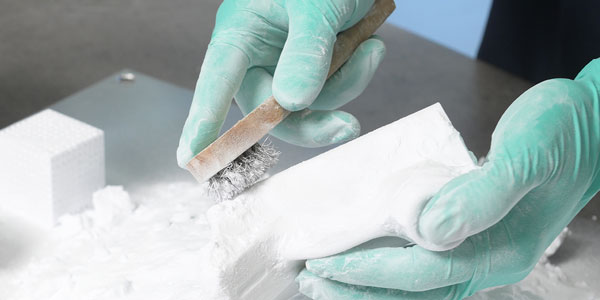
Für das Selektive Laserschmelzen (SLS) arbeiten wir an smarten Prozessüberwachungen. Diese sollen es ermöglichen, in den laufenden Prozess einzugreifen und gegebenenfalls nachzusteuern. Hierdurch wollen wir Wärmestaus verhindern und das gesamte Pulverbett zuverlässig als Druckbereich nutzbar machen. So wollen wir aufwendige und zeitintensive Fehldrucke vermeiden. Wir entwickeln Prozesse für die Pulver-basierte Additive Fertigung mit dem Laser weiter, um sie für neue Anwendungen oder Materialien anzupassen.
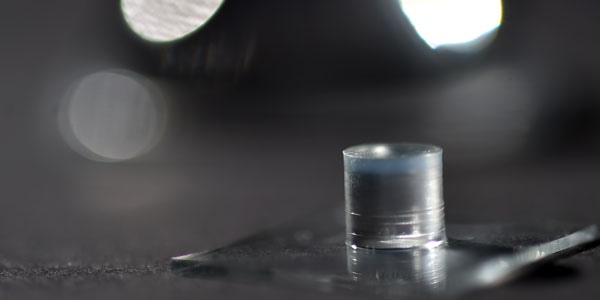
Wenige Produkte bestehen nur aus nur einem Material. Um auch Multimaterialbauteile additiv herstellen zu können, entwickeln wir Prozesse, mit denen sich verschiedene Werkstoffe kombinieren lassen. Im Fokus steht dabei zum einen, artgleiche Werkstoffe miteinander zu kombinieren, aber auch metallene Bauteile mit Kunststoff zu vereinen. Außerdem arbeiten wir an gradierten Werkstoffen, um flexibel die Härte und Zusammensetzung eines Bauteils zu variieren.
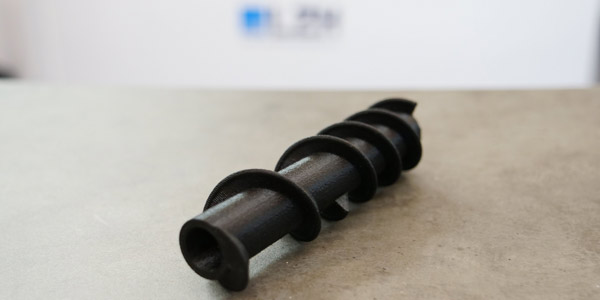
Bei der Filament-basierten Additive Fertigung (eng.: Fused Deposition Modelling, FDM) beschäftigen wir uns mit der Topologie-Optimierung und der Prozessentwicklung, um neue Materialien für den 3D-Druck zu qualifizieren. Im Fokus stehen dabei nachhaltige Naturfaser-basierte oder kompostierbare Werkstoffe. Mit Hochleistungsfaserverbundstrukturen wollen wir neue Herstellungsverfahren für den Leichtbau schaffen. Außerdem arbeiten wir daran, 3D-gedruckte Elemente mittels Laserdurchstrahlschweißen stoffschlüssig zu verbinden. Bauteile aus dem Filamentdruck sind vielseitig einsetzbar, u.a. sogar für Fassadenverkleidungen in der Architektur oder als Furnier auf Möbeln. Wir arbeiten insbesondere an:
• Faserverbundstrukturen
• Kurz- und Endlosfaserverstärkten Werkstoffen
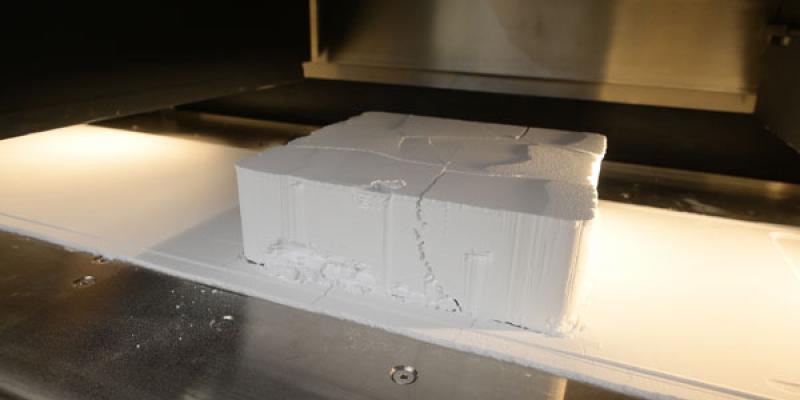
Um die Additive Fertigung weiter in der Industrie zu etablieren und neue Anwendungsmöglichkeiten zu erschließen, arbeiten wir an und mit neuen Materialien. Dafür entwickeln wir neue Prozesse oder optimieren bestehende. Um optimale Eigenschaften zu erreichen, analysieren und charakterisieren wir die Bauteile genau und passen die Prozesse entsprechend an.
Wir arbeiten mit:
• leitfähigen Materialien
• nachhaltigen und kompostierbaren Naturmaterialien
• Kohlenstofffasern für Faserverbundstrukturen
• transparenten Photopolymeren
• hybriden Materialien (organisch-anorganisch)
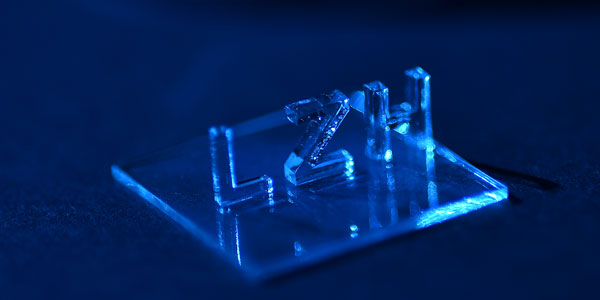
Wir arbeiten an der Weiterentwicklung hochauflösender 3D-Druckverfahren, um deren Potential für die generative Fertigung multiskaliger Strukturbauteile oder auch komplexer Komponenten zu erschließen. Neben Laser-basierten Technologien im Polymerbad wie der Stereolithographie und der Zwei-Photonen-Polymerisation nutzen wir Mikro-Dispenser und den Aerosol Jet sowie hybride Verfahren. Damit dispensieren wir zum Beispiel Leiterbahnen und optische Polymere. Um die Potentiale für den industriellen Einsatz zu erweitern, erarbeiten wir Strategien zur Automatisierung von Prozessketten.
Glas & Keramik
Mit der Additiven Fertigung von Glas und Keramik werden zukünftig neue Anwendungsfelder, beispielsweise im chemischen Apparatebau, der Architektur oder sogar der Optik, erschlossen. Wir arbeiten deshalb an der Weiterentwicklung der Fertigungsprozesse, um reproduzier- und automatisierbare Glaskomponenten mit einer hohen Komplexität und optischen Qualität herzustellen.
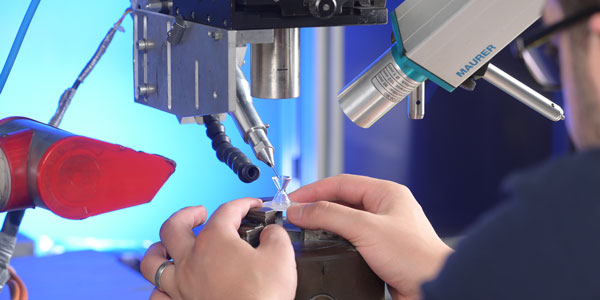
Das von uns mitentwickelte Verfahren zur additiven Glasfertigung, auch Laser Glass Deposition genannt, ermöglicht mithilfe eines faserbasierten Prozesses automatisiert komplexe Strukturen herzustellen. Im Fokus steht dabei die Automatisierung des umfangreichen Handlings, vom Umgang mit dem Rohwerkstoff bis zum fertigen Produkt für standardisierte, reproduzierbare Ergebnisse. Des Weiteren arbeiten wir an der Additiven Fertigung von Optiken und optischen Komponenten wie beispielsweise Kugellinsen. Wir können an bestehende Komponenten andrucken sowie schichtweise unabhängige Bauteile aufbauen.
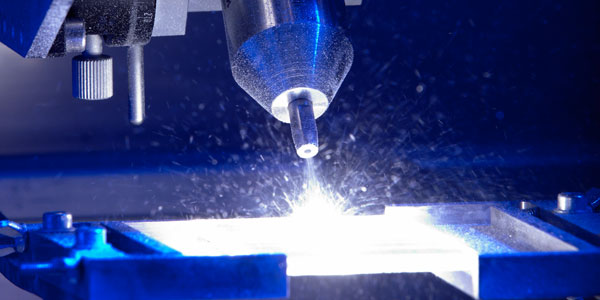
Keramische und Glaswerkstoffe können im Pulverbettverfahren additiv zu Bauteilen verarbeitet werden. Wir erforschen neben der Herstellung kompletter Bauteile die gezielte Modifikation elektrischer Eigenschaften durch das Dispergieren von Keramikpartikeln in Metall beim Laserauftragschweißen. Außerdem beschäftigen wir uns mit dem Gradieren mit Wolframkarbiden im Laserbeschichtungsprozess, um die Standzeit von Werkzeugen signifikant zu verbessern.
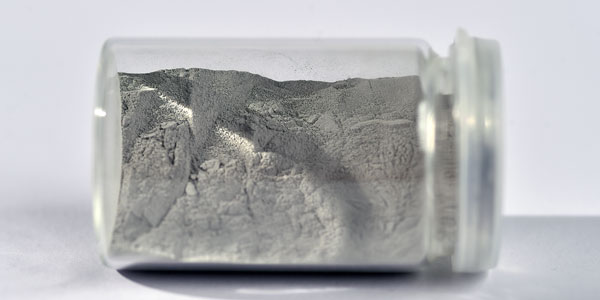
Um mehr Anwendungen für die Additive Fertigung von Gläsern und Keramiken zu ermöglichen, entwickeln und evaluieren wir Prozesse für Werkstoffe, die dafür bisher noch nicht eingesetzt werden. Von großem Interesse für die Optik, aber auch den Glasapparatebau, ist die Verarbeitung von Quarzglas und Borosilikatglas. Für keramische und Glaswerkstoffe entwickeln wir die Prozesse derzeit weiter. Außerdem arbeiten wir daran, die additive Verarbeitung des weit verbreiteten Kalk-Natron-Glases erstmals zu ermöglichen.
Konstruktion & Produktdesign
Mit den generativen Fertigungsverfahren werden viele Einschränkungen bei der Konstruktion überwunden. Doch nicht jedes Design eignet sich für die Additive Fertigung. Wir entwickeln smarte Konstruktionen und optimieren Bauteile, die die Möglichkeiten der Additiven Fertigung voll ausschöpfen und material- und aufwandsoptimiert sind. Außerdem beschäftigen wir uns mit Optomechanik.
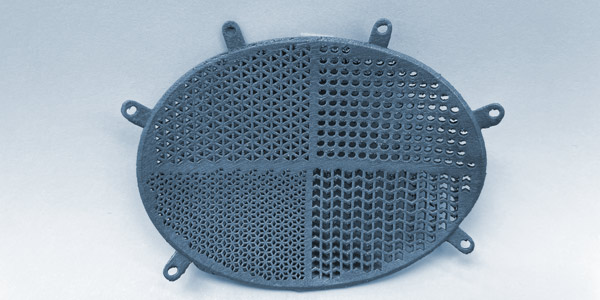
Die Additive Fertigung ermöglicht nahezu komplette Designfreiheit. Aber jedes additive Verfahren hat seine Eigenheiten, die in der Konstruktion der individuellen Bauteile berücksichtigt werden müssen, um Material, Druckzeiten und Nachbearbeitung möglichst gering zu halten. Daher arbeiten wir an der smarten Konstruktion von Bauteilen, deren optimaler Ausrichtung im Bauraum sowie dem optimalen Einsatz von Stützstrukturen.
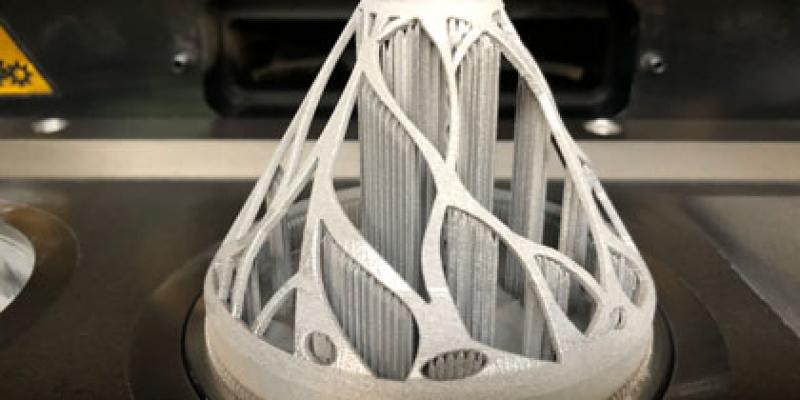
Material und Gewicht sparen sowie Druckzeiten herabsetzen bei gleichbleibender Belastungsfähigkeit - die Topologieoptimierung lohnt sich für viele Bauteile. Wir berechnen die beste Kräfteverteilung und optimieren den Materialeinsatz. Wir beschäftigen uns außerdem mit automatisierten Lösungen, um zukünftig Topologieoptimierung mit Konstruktionsrichtlinien zu kombinieren und zum besten Produktdesign eines individuellen Bauteils zu kommen.
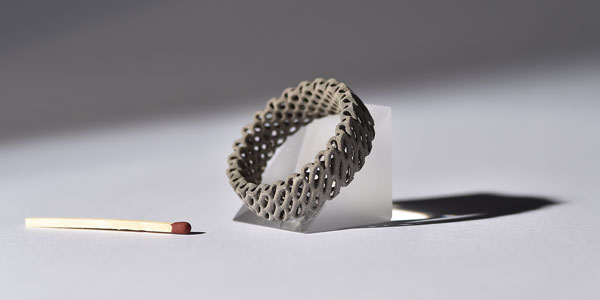
Für den Leichtbau aus dem 3D-Drucker erarbeiten wir Prozesse mit Werkstoffen wie Magnesium und optimieren das Design durch geschickte Konstruktion und Topologieoptimierung. Magnesium ist mechanisch belastbar, bioresorbierbar und hat dennoch eine geringe Dichte. Zudem eignet es sich vor allem für den Einsatz in innenliegenden Strukturen. Dabei beschäftigen wir uns außerdem damit, Prozesse für schwer verarbeitbare Werkstoffe zu entwickeln, zu optimieren und industriell einsetzbar zu machen.
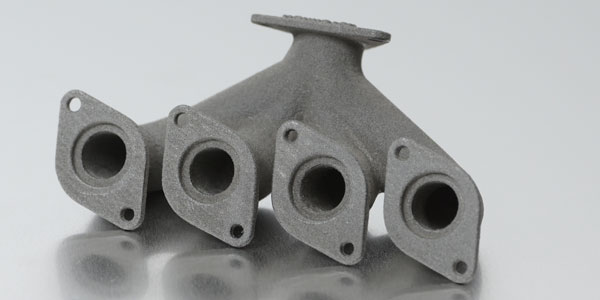
Kühlkanäle direkt an der Kontur, mit Kurven und Winkeln oder innenliegende Halterung - mit der Additiven Fertigung können Funktionen optimal in Bauteile integriert werden. Wir optimieren Bauteile für die additive Fertigungsweise und entwickeln die dazu passenden Prozesse. Dabei beschäftigen wir uns auch damit, wie spezielle neue Komponenten ausgelegt werden können. Eine neue Komponente kann dabei mehrere einzelne Komponenten vereinen.
Anlagen- und Systemtechnik
Prozesse sind häufig nur so gut, wie das Equipment auf dem sie laufen. Wir entwickeln daher Anlagen- und Systemtechnik immer mit Blick auf konkrete Anwendungen, die Fähigkeit zur Integration in bestehende Anlagen und Industriereife. Unser Spektrum reicht dabei von einzelnen Systemkomponenten bis hin zu Anlagenkomponenten oder kompletten Maschinen.
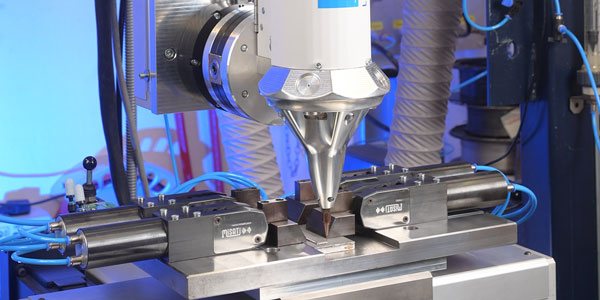
Unsere Prozessentwicklung ergänzen wir durch eigene Laserbearbeitungsköpfe, um die besten Lösungen für innovative Anwendungen zu finden - einsatzbereit für die industrielle Anwendung. Zu unseren bisherigen Entwicklungen gehören koaxiale Bearbeitungsköpfe für das Auftragschweißen, mit denen verschiedene Materialien richtungsunabhängig verarbeitet werden können. Dabei lassen wir Erkenntnisse aus der Forschung beständig in die Weiterentwicklung der Systemkomponenten einfließen.
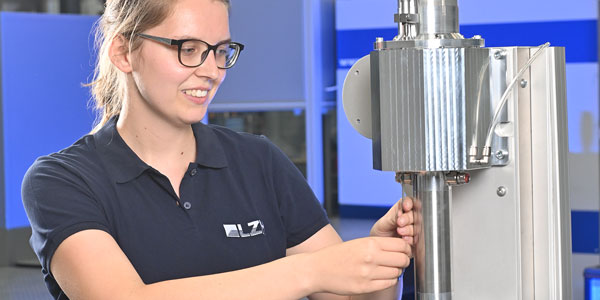
Additive Fertigungsprozesse stehen selten losgelöst im Produktionsumfeld. Wir arbeiten an der Integration und Anbindung unserer entwickelten Komponenten in bestehende Maschinen und Anlagen. Außerdem forschen wir daran, Verfahren miteinander zu kombinieren. Zum Beispiel entwickeln wir Maschinen, die additive und subtraktive Prozesse kombinieren, für schnellere Fertigungs- und weniger Standzeiten. Weiterhin beschäftigen wir uns damit, die Produktion in einer Sauerstoff-freien Umgebung möglich zu machen.
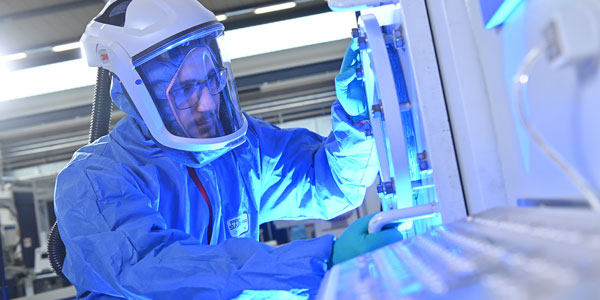
Die Additiven Fertigung bringt neue Herausforderungen an die Anlagen- und Arbeitssicherheit mit sich. Wir entwickeln Strategien für den sicheren Umgang mit Pulvern oder Förderstrecken für die Integration in die Fertigung und beschäftigen uns mit dem Monitoring von Prozessemissionen. Unser Fokus liegt dabei darin Pulververschleppung zu vermeiden. Dafür erforschen wir die Wege der Pulververschleppung bis hinein ins private Umfeld und zeigen Vermeidungsstrategien auf.
Monitoring und Qualitätssicherung
Für eine Produktion möglichst ohne Fehler und Ausschuss forschen wir an smarter Prozessüberwachung mit Echtzeit-Regelung. Dadurch soll die Additive Fertigung verlässlicher, kostengünstiger und somit noch attraktiver werden. Wir nutzen zerstörungsfreie Charakterisierungs- und Analysemethoden, können damit Bauteile mit ihrem digitalen Zwilling abgleichen und mit Hilfe von künstlicher Intelligenz Prozesse weiter verbessern. Die Prozessüberwachung und Qualitätssicherung ist damit ein wesentlicher Teil unserer Forschung für die „First-Time-Right“-Strategie.
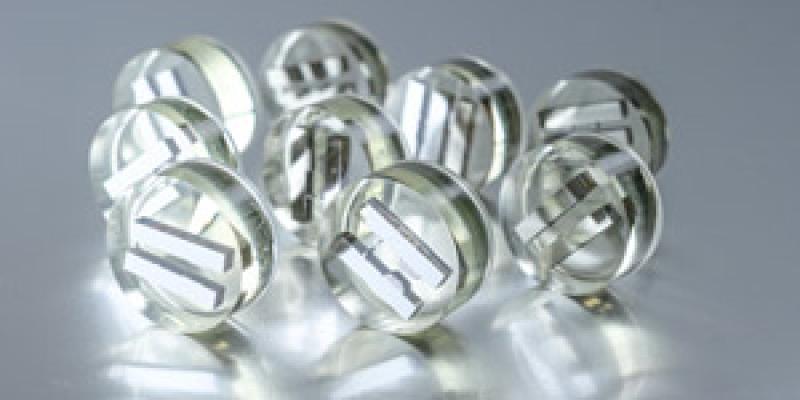
Um die Qualität additiv gefertigter Bauteile beständig zu erhöhen, entwickeln wir entsprechende Charakterisierungsmethoden für Pulver und Bauteile. Pulver untersuchen wir vor dem Druck auf Partikelform, -größe sowie ihre Schütt- und Klopfdichte. Fertige Bauteile analysieren wir anhand verschiedener Methoden auf Porenbildung, Schichtdicke und ihre Tauglichkeit u.a. durch Härteprüfungen. Wir entwickeln zerstörungsfreie Analysen mit Optischer Kohärenztomographie (OCT) und Emissionsanalysen. Uns stehen weiterhin Rasterelektronenmikroskopie (REM), ein Nano-Computertomograf sowie Energiedispersive Röntgenspektroskopie (EDX) zur Verfügung. In Kombination mit einer Online-Prozesskontrolle wollen wir so eine „First-Time-Right“-Strategie umsetzen, also eine Additive Fertigung möglichst ohne Ausschuss.
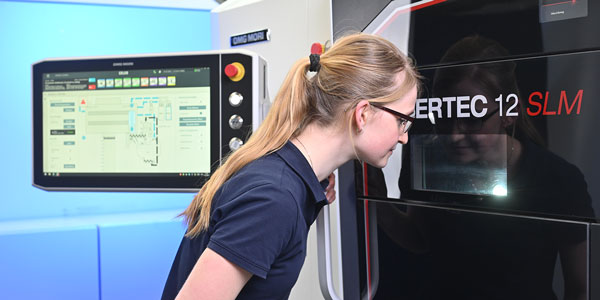
Durch die Überwachung des laufenden Druckprozesses wollen wir zukünftig flexibel in den Druck eingreifen und nachsteuern können. Wir entwickeln Monitoringsysteme weiter und beschäftigen uns mit deren Integration in die Druckprozesse sowie in die Nachbearbeitung. Wir nutzen:
- Hyperspektralkameras, um Verunreinigungen zu erkennen und die Rauigkeit von Oberflächen vorhersagen
- Pyrometrie
- Thermografie
- Sauerstoffgehaltmesser
Ziel ist, in Zukunft Fehler direkt beim Entstehen der Schichten zu erkennen und so fehlerhafte Bereiche ausgleichen zu können. Dafür erarbeiten wir Feedback-Loops und nutzen künstliche Intelligenz, um die Ausschuss-freie Additive Fertigung zu realisieren.
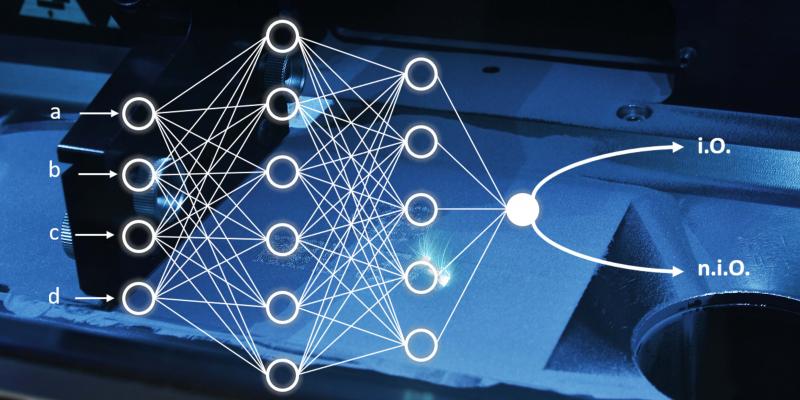
Der Mehrwert künstlicher Intelligenz in der Additiven Fertigung geht weit über die Überwachung hinaus. Wir arbeiten an selbstlernenden Systemen, die zukünftig den Prozess aktiv steuern und so Fehler vermeiden oder ausgleichen. Grundlage dafür sind ein tiefes Prozessverständnis und die umfassende Aufnahme der Prozessdaten. Mittels Bildverarbeitung und Feature-Erkennung kann maschinelles Lernen Bauteile klassifizieren und beispielsweise Oberflächenrauheiten vorhersagen.