Oxygen is a disruptive factor in many production processes within the metalworking industry: Oxide layers formed during metal processing in the presence of oxygen can hinder the joining of workpieces and accelerate the wear of components and tools. In the Collaborative Research Center (CRC) 1368 "Oxygen-Free Production," researchers employ an innovative method to address the oxidation problem. They introduce argon protective gas with a small amount of silane during production. Silane reacts with the surrounding oxygen, creating an atmosphere equivalent to an XHV environment. This atmosphere has an extremely low oxygen content similar to that in an extremely high vacuum. This oxygen exclusion approach is significantly more cost-effective than implementing a technical vacuum. At LZH, scientists are researching this method for powder-bed-based laser beam melting and laser beam brazing.
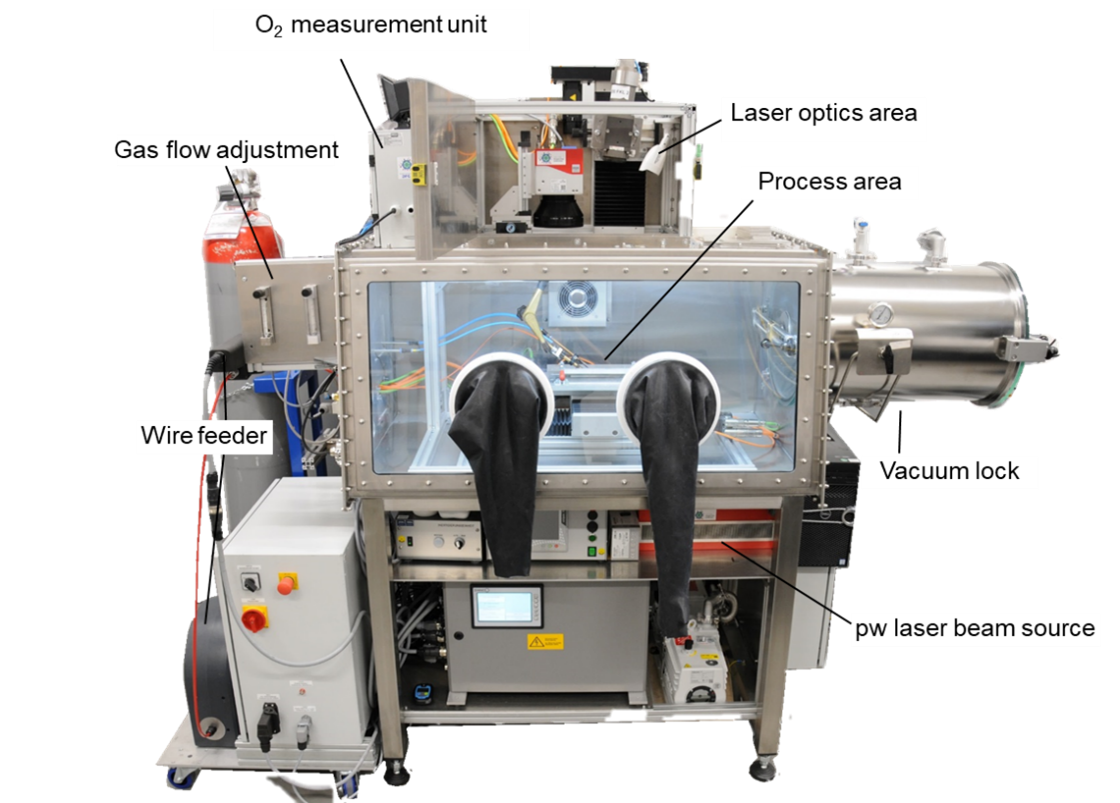
Goal: Laser Beam Brazing Without Flux
In a subproject, the group Joining and Cutting of Metals has developed a novel brazing process that eliminates the need for flux. Fluxes, which are partly environmentally and health-hazardous, are typically used to break up the oxide layer on the material surface, allowing metal and filler material to react. In the newly developed process, LZH researchers break the oxide layer with a ns-pulsed laser beam source instead. Subsequently, the brazing process occurs under a continuous-wave (cw) laser beam in a silane atmosphere. The oxygen-free atmosphere prevents re-oxidation of the surface between process steps.
Researchers have demonstrated the ability to permanently remove the oxide layer on aluminum alloys in an oxygen-free atmosphere. Consequently, wetting the surface with a compatible solder material was possible. In the second funding period, researchers will transfer the process to the challenging mixed connection of aluminum and copper and explore the process limits.
Additive Manufacturing in an Oxygen-Free Atmosphere
The Additive Manufacturing - Metals group investigates how metal powders can be processed in an oxygen-free atmosphere using laser-based powder bed fusion of metals (PBF-LB/M). The process was developed using the titanium alloy Ti-6Al-4V on a specially developed system for the PBF-LB/M process and monitored using high-speed cameras.
The subproject's goal is to gain a fundamental understanding of the process in an oxygen-free atmosphere and the influence of oxygen. Researchers expected the absence of oxygen to result in a more stable process, fewer splatters, and improved component properties. They demonstrated that not only did the number of splatters decrease, but they also oxidized less, reducing powder degradation. However, for further improvement of the process and component quality, eliminating moisture in the atmosphere and powder will be thoroughly investigated in the second funding period.
About CRC 1368
In the Collaborative Research Center (CRC) 1368 "Oxygen-Free Production" the LZH collaborates with eight institutes at Leibniz University Hannover, four institutes at Clausthal University of Technology, and the Chair of Data Management in Mechanical Engineering at the University of Paderborn. The CRC is funded by the German Research Foundation (DFG), with the second funding period supported with approximately €10.5 million until the end of 2027.
Laser Zentrum Hannover e.V. (LZH)
As an independent, non-profit research institute, the Laser Zentrum Hannover e.V. (LZH) stands for innovative research, development, and consulting. Supported by the Lower Saxony Ministry of Economics, Transport, Construction and Digitalization, the LZH is dedicated to selflessly promoting applied research in the field of photonics and laser technology. Founded in 1986, almost 200 employees are now working at the LZH.
The LZH offers solutions to current and future challenges with its smart photonics. Along the process chain, natural scientists and engineers work interdisciplinary together: from component development for specific laser systems or for quantum technologies to process developments for a wide variety of laser applications, for example for medical and agricultural technology or lightweight construction in the automotive sector. 19 successful spin-offs have emerged from the LZH to date. Thus, the LZH creates a strong transfer between fundamental science, application-oriented research, and industry - and uses light for innovation.