With innovative approaches, the LZH is pushing the boundaries of what is possible in Additive Manufacturing and opening up new perspectives for industrial production.
Powder bed-based additive manufacturing: Focus on special materials and manufacturing in space
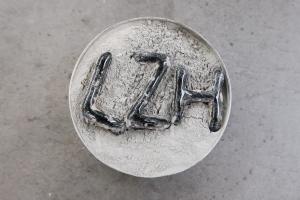
In the field of powder bed-based Additive Manufacturing with metallic materials the LZH focuses on process development of special materials such as magnesium and its alloys, brass and miobium. These materials offer special properties for applications, that place high demands on biocompatibility, thermal conductivity or strength. At formnext the LZH features components that could be used for an efficient hydrogen incineration, and how 3D-print could look like on the moon.
Wire-based deposition welding: efficient and divers
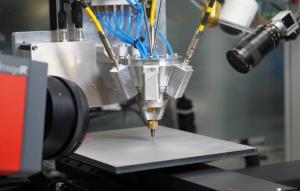
Another highlight of the trade fair presentation is wire-based deposition welding, which is especially used for cost-efficient manufacturing of large-scale components. Thanks to a specially developed laser processing head for coaxial build-up welding, it is possible to precisely manufacture very large and small components in complex geometries, regardless of direction. This technique also enables manufacturing of multi-material-components, for which cost-effective basic materials are provided with hard coatings.
System technologies for Additive Manufacturing
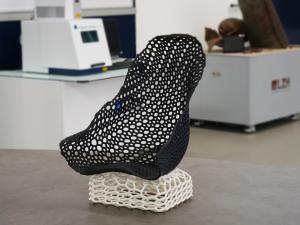
In the field of Additive Manufacturing with polymers the LZH shows innovative solutions for systems engineering. Cost-effectively produced additively manufactured components can for example be used in vulnerable areas and just replaced if damaged. The LZH is exhibiting a system that has been successfully used in a research project to defuse unexploded bombs. The LZH is also demonstrating how Additive Manufacturing can be used productively in the field of medical technology with a seat orthosis for physically disabled children.
Glass manufacturing: automation and new applications
Another research area at the LZH is the Additive Manufacturing with glass filament. The aim is to push the boundaries of conventional glass manufacturing to achieve new possibilities in areas such as structural glass engineering, optics/photonics or medical technology. The research group Glass at the LZH is working on producing voluminous and dense glass components with a smooth surface and homogeneous volume. This ensures optimized load transfer and the possibility of producing free-form lenses.
LZH and Niedersachsen ADDITIV as partners for research and development
The Laser Zentrum Hannover e.V. supports companies as a strong partner for research and development work in the field of Additive Manufacturing. With its expertise in the processing of metal, polymers and glass, the LZH supports companies in the implementation of innovative production processes and the development of pioneering technologies. The experts from Niedersachsen ADDITIV are also on site and are available as contacts for SMEs from Lower Saxony.
Laser Zentrum Hannover e.V. (LZH)
As an independent, non-profit research institute, the Laser Zentrum Hannover e.V. (LZH) stands for innovative research, development, and consulting. Supported by the Lower Saxony Ministry of Economics, Transport, Building and Digitalization, the LZH is dedicated to selflessly promoting applied research in the field of photonics and laser technology. Founded in 1986, almost 200 employees are now working at the LZH.
The LZH offers solutions to current and future challenges with its smart photonics. Along the process chain, natural scientists and engineers work interdisciplinary together: from component development for specific laser systems or for quantum technologies to process developments for a wide variety of laser applications, for example for medical and agricultural technology or lightweight construction in the automotive sector. 18 successful spin-offs have emerged from the LZH to date. Thus, the LZH creates a strong transfer between fundamental science, application-oriented research, and industry - and uses light for innovation.